PREPARING FOR CHANGE
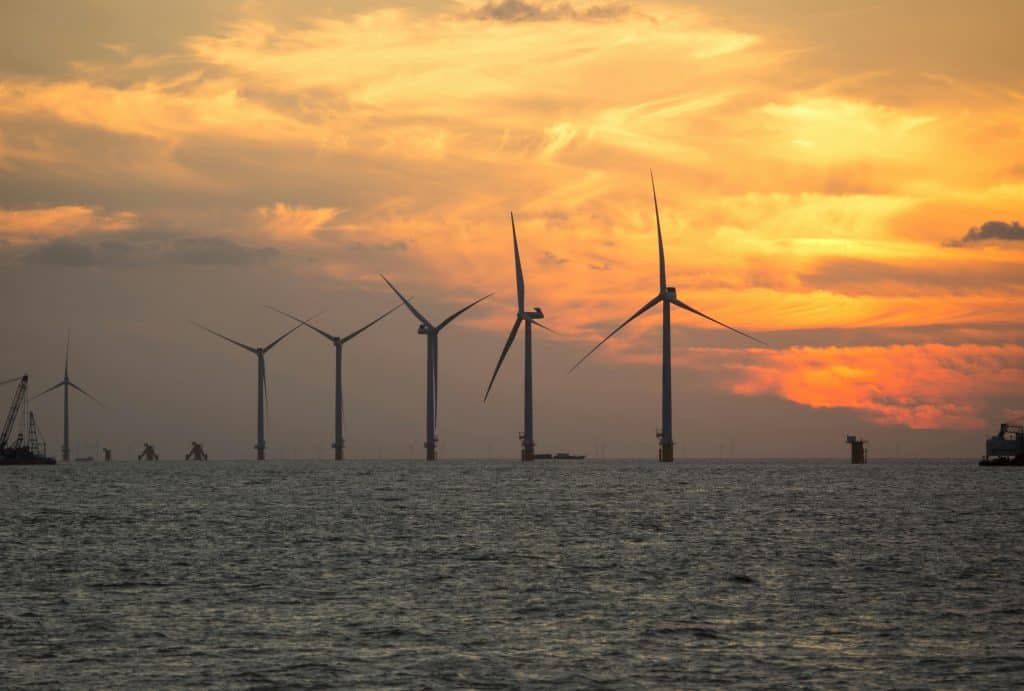
RESISTORS HELP TO GET THE MOST OUT OF WIND POWER
In January 2025, the UK government announced new measures to unlock up to thirteen major wind projects as part of its Plan for Change. But with wind curtailment — the switching off of wind turbines — reaching record levels in 2024, how can we make the most of the energy generated? Here, Mike Torbitt, managing director of Cressall, explores the role that resistors can play in preventing the wastage of wind power.
The government’s Plan for Change aims to modernise the ‘outdated and archaic’ infrastructure regulations to increase the pace at which offshore wind projects are constructed. In total, the measures could generate up to 16 Gigawatts (GW) of electricity and around £20-30 billion of clean energy investment.
The announcement is promising, but much of the newly harnessed wind power could be wasted. Turbines are frequently turned off in periods of high wind, to protect the grid system from being overwhelmed by the power generated.
According to a report from electricity supplier Octopus, enough energy was wasted in the first nine months of 2024 to power two million UK homes for a year. Not only does wind curtailment limit the UK’s ability to fully transition to clean energy, but it also results in higher bills for consumers.
And the problem is growing — the costs of wind curtailment will reach £3.7 billion by 2030. As the UK continues to invest in wind power, it’s important that additional energy generated is put to good use. So, why is energy being wasted and how can this be prevented?
DISTANCE ISSUES
The key reason for switching off wind turbines is distance — both from the grid and from demand.
Offshore farms are much further from the grid than their onshore counterparts, meaning there are less readily available connection points to distribute power to the transmission network. Consequently, in the case of strong winds, there are fewer options available to distribute the energy elsewhere.
The remote location of offshore windfarms also means they are located far from high-demand areas. For example, Scotland currently has seven operational offshore windfarms, many of which are located near the north of the country where population density is low. Demand for energy is greater elsewhere, but inefficient cable networks mean that a lot of power is lost during transmission.
HANDLING THE EXCESS
Energy experts have several suggestions on how to tackle wind curtailment. For instance, the Octopus report recommends zonal pricing, which means that people living near turbines can benefit from cheaper energy rather than it going to waste. The research suggests that businesses could save in the region of 65 to 99 per cent on energy costs by moving to Scotland and benefitting from zonal pricing. While the prospect of lower bills would hopefully encourage people to welcome the development of renewable energy projects within their communities, moving to energy-abundant areas isn’t feasible for all businesses.
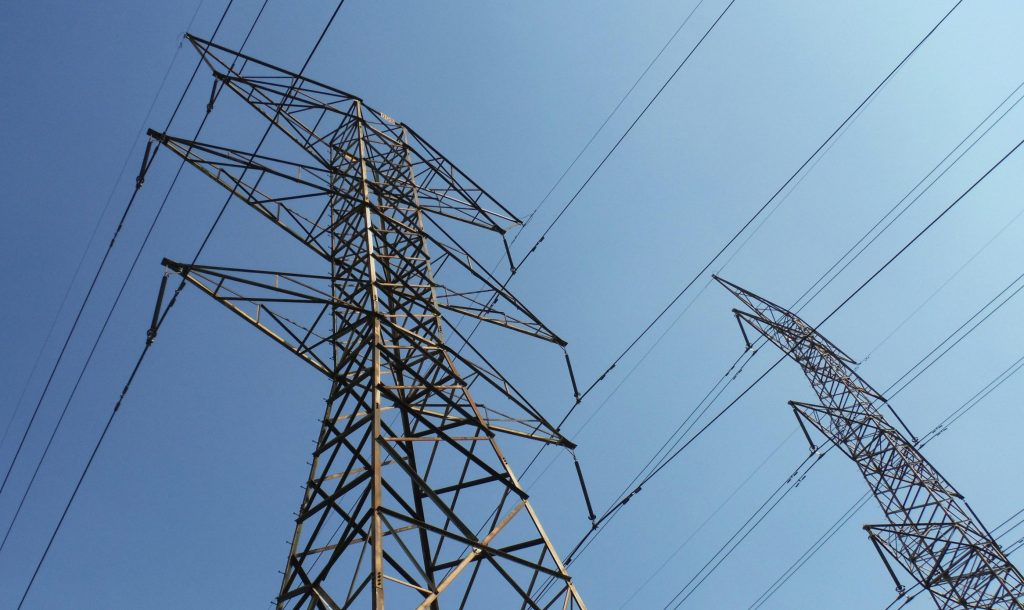
Another way to minimise wastage is by improving the infrastructure that transmits energy from offshore sites to high-demand areas. In March 2025, construction will begin on the Eastern Green Link 1 (EGL1), which will enable the transmission of energy from Torness in Scotland to Hawthorn Pit in the North East of England. Once complete, the high-voltage direct current (HVDC) project will deliver enough electricity for two million homes.
HVDC enables efficient power transmission over long distances between offshore wind farms and the grid, thanks to its consistent current density. Resistor technology is essential in HVDC systems, safeguarding against grid failures by absorbing excess wind energy until the transfer is safely halted. Additionally, DC neutral earthing resistors provide further protection to the system, both onshore and offshore, within HVDC converter transformers.
Cressall has extensive experience in supplying resistors for renewable projects, including a GE Vernova partnership covering five HVDC projects in the North Sea.
The government’s aim to amend inflexible planning restrictions and boost wind power generation projects through its Plan for Change initiative is a welcome development. However, to create real change, the rollout of energy transmission projects must keep pace with offshore wind developments. HVDC systems supported with reliable resistor technology will enable the UK to reduce wind curtailment and make the most of the renewable resources available.
CRE66