ELECTRIC VEHICLES’ UNSUSTAINABLE LITTLE SECRET
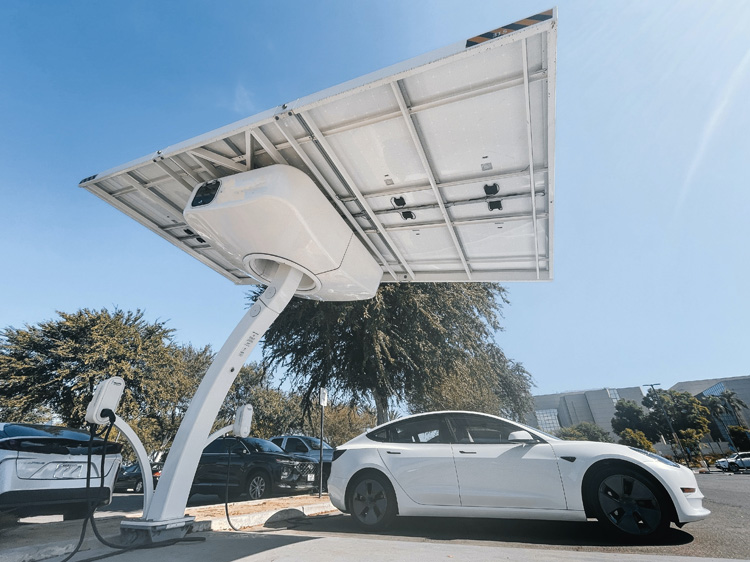
BATTERIES ARE THE WEAKEST LINK IN THE SUSTAINABILITY CHAIN
Electric vehicles (EVs) have been heralded as the answer to transportation’s sustainability issues, providing a scalable solution for the notoriously difficult-to-decarbonise sector. However, there’s one key component that needs some work if EVs are to become a completely sustainable method of transport — the battery. Here, Simone Bruckner, managing director of automotive resistor manufacturer Cressall, investigates the dark side of EV batteries.
The electrification of the automotive market is a necessary step to reduce greenhouse gas emissions and ward off climate change’s consequences. Every automaker is in support of the rollout, with more affordable models being released by the day to encourage consumers to make the electric shift. At the same time, governments are enforcing change through legislation that bans the sale of new fossil fuelled vehicles from as early as 2025.
The urgency of the climate crisis and looming legislation changes has resulted in the exponential growth of the EV market. A recent McKinsey report estimates that by 2035, the three largest automotive markets — the European Union, United States and China — will be fully electric. However, while driving an EV is ‘zero emission’, an unsustainable secret hides in production.
THE PROBLEM WITH BATTERIES
Traditional diesel and petrol-powered vehicles benefit from lead-acid batteries, which are widely recyclable. However, the same can’t be said for EVs, which use lithium-ion batteries instead. Typically made from raw materials including cobalt, nickel and manganese, lithium-ion batteries are extremely expensive to produce and require high levels of mining activity.
Mining raw materials can lead to huge environmental destruction, releasing elements into the atmosphere that can contaminate soils and disrupt entire ecosystems. What’s more, lithium-ion batteries are significantly more challenging to recycle, contributing to further environmental damage if improperly disposed of at the end of their life.
Aside from environmental devastation, lithium-ion batteries are also in short supply. Battery production capacity across the globe is expected to increase twenty-fold, but this won’t be enough to meet the expected future demand.
Although several industry players are developing recycling methods and reducing the reliance on raw materials, any significant progress is far off. For now, to ensure demand is met and improve the output for using these materials, it’s important for automakers to consider how they can make existing batteries last longer.
EXTENDING LIFESPAN
Automotive design engineers should consider the benefits that regenerative braking can bring in extending lithium-ion battery lifespan. A study by the Institute for Electrical Energy Storage Technology concluded that a higher level of regenerative braking usually reduces battery ageing by reducing lithium plating.
Lithium plating refers to the accumulation of metallic lithium on the battery’s anodes, which can cause irreversible damage over time and significantly reduce battery lifespan. Lithium plating is exacerbated long charging periods, but regenerative braking can help to alleviate this issue.
Regenerative braking occurs when an EV recovers energy while decelerating by using its electric motor as an electric generator and converting kinetic energy into electrical energy. This electrical energy is then stored in the vehicle’s battery, increasing range and efficiency between charges. Incrementally recharging the battery each time the vehicle brakes reduces the length of the charging period, therefore reducing the accumulation of metallic lithium and improving battery operations and life cycle.
Resistors play a crucial role in regenerative braking, by removing excess energy from the system in the event that the battery is already fully charged. This prevents overcharging or catastrophic damage to the system. Cressall’s EV2 resistor is designed specifically for EV applications and is the most compact and lightweight dynamic braking resistor model on the market, making it ideal for EVs.
EVs are central to a more sustainable transportation system but we mustn’t cite them as an answer to all of our environmental issues. Recognising the problems that they bring and considering both long and short-term solutions is necessary in order to create truly sustainable transportation. While lithium-ion battery recycling could be a viable option in the future, extending battery life through techniques such as regenerative braking is essential to see us through and reduce reliance on finite raw materials from today.
CR474