WATER VERSUS CONVECTION COOLING — WHAT’S THE DIFFERENCE?
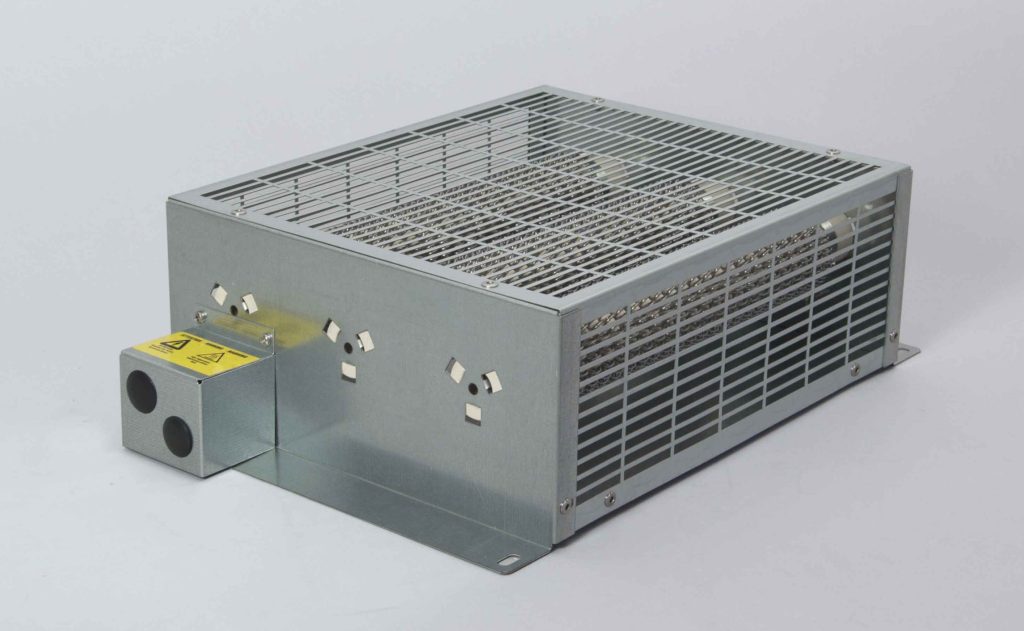
CHOOSING THE RIGHT COOLING SYSTEM FOR YOUR APPLICATION
For applications relying on an electrical drive system, such as those in the marine and automotive sectors, overheating poses serious risks to equipment performance. Employing an appropriate cooling system helps to safeguard equipment, but knowing what to look for can be tricky. Here, Mike Torbitt, managing director at resistor manufacturer Cressall, explains the differences between water and convection cooling and how to determine the best-suited system.
When engines operate significantly above their optimum working temperature for long periods of time, they are at risk of engine failure due to overheating. Excessive heat not only reduces the ability of lubricants to protect engine parts from wear and tear, but it can also lead to thermal shock. This phenomenon occurs during rapid temperature changes, causing application components to expand and contract at different rates, resulting in cracks and fractures.
There are several steps you can take to protect against overheating. Firstly, it’s important to understand that optimum operating temperatures differ between applications. For example, the ideal temperature for car engines ranges between 75 and 105 degrees Celsius, while for boats this can vary depending on engine type. Selecting dynamic braking resistors (DBRs) with insulated components can help to prevent thermal shock, but employing an effective cooling system is also essential in avoiding overheating.
However, with both water and convection cooling options to choose from, it can be difficult to select the right cooling system for your resistor. So, what’s the difference?
CONVECTION VERSUS WATER-COOLED DBRS
While both options require minimal maintenance and are cost-effective to run, there are several key differences between air and water-cooled resistors.
Convection cooling, also known as air cooling, refers to the transfer of heat into the ambient air using airflow. There are two types of convection cooling systems available: natural and forced convection.
Natural convection relies on the buoyancy effect to cool the application. Since warm air is less dense than cool air, it naturally rises upwards away from the heat source and is replaced by cool air. Natural convection is therefore able to generate a consistent air flow without the need for ventilation mechanisms in applications where the ambient airflow meets thermal demands.
However, where increased heat transfer is required, forced convection cooling is preferable. Since forced convection uses fans, more air can be moved through the system in the same amount of time.
Despite generally being more effective than natural cooling, forced convection also has its limitations. Fans can be noisy and take up a lot of space, meaning they are not well suited to compact applications.
Consequently, water cooling often provides a more effective solution. Not only does the water-cooling method use less space and energy than convection cooling, but it is also better suited to applications with higher continuous power requirements. Since liquid has a higher density than air, it has a higher capacity for heat carrying.
MARINE COOLING
Water-cooled DBRs are especially useful in maritime applications. Cooling often proves difficult as the drive system is usually placed within the ship’s innermost parts and surrounded by heat-sensitive equipment.
To tackle this, most vessels use a chilled water system for machinery cooling and air conditioning. Adding resistors into systems such as the closed air/ closed water (CACW) is relatively simple and allows for up to 95 per cent of the energy from a DBR to be transferred to the ship’s water supply. This recirculation protects the equipment in the machinery room from detrimental ambient temperature increases.
Some marine applications also utilise a sea water cooling system. Provided the DBR is coated in a suitable material such as titanium to safeguard against erosion, this method is a sustainable way of reducing fresh water usage.
Cressall has several decades of experience in designing and manufacturing convection and water-cooled DBRs for applications ranging from automotive and railways to cranes and maritime. In addition to matching continuous power requirements of up to 1500 kilowatts (kW) for convection-cooled DBRs and up to 1800 kW for water-cooled DBRs, Cressall also offers custom options tailored to individual applications.
Safeguarding your application from heat is crucial but proves challenging without a thorough understanding of the different cooling methods available. Choosing a reliable convection or water-cooled DBR provides the assurance that your equipment is protected against overheating.
To discuss the right cooling system for your application, get in touch with our expert team.
CRE658