A TRANSCONTINENTAL RENEWABLE NETWORK?
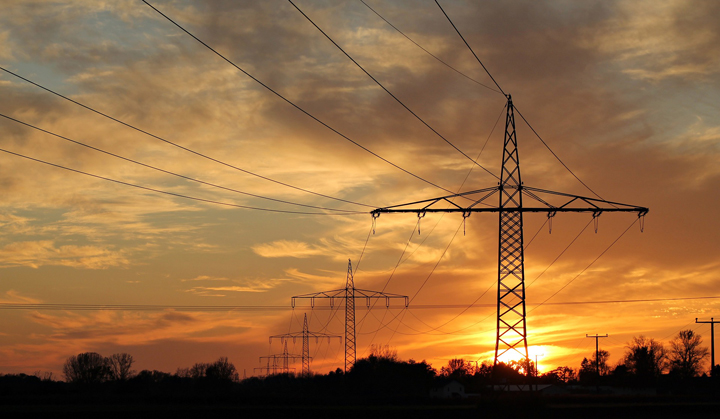
HOW HIGH VOLTAGE DIRECT CURRENT TRANSMISSION COULD TRANSFORM POWER SUPPLY
The SuperSmart Grid (SSG) is a theoretical concept that involves the creation of a transcontinental electricity network connecting Europe, the Middle East and North Africa to deliver low cost, high capacity, low loss electricity. To support global efforts to decarbonise power generation, could the SSG become a reality?
The SSG is a fusion of a super grid, a wide-area, often transcontinental transmission network and a smart grid, which uses digital technology, such as smart meters, to react to fluctuations in energy demand.
By implementing this system across Europe, the Middle East and Africa, this geographical area could benefit from an entirely renewable energy supply, which in turn supports the United Nations’ Sustainable Development Goal Seven: ensure access to affordable, reliable, sustainable and modern energy for all.
Offshore wind farms and solar power are the two resources that offer great potential, given the large number of suitable sites for both systems throughout the region. Having identified potential energy resources, how can this energy be transmitted to meet demand over such a vast area?
DEVIATING FROM THE AC NORM
High voltage direct current (HVDC) uses direct current (DC) for most electrical power transmission. Although DC is less common than standard alternating current (AC) systems, it meets the demands of the SSG for a variety of reasons.
HVDC transmission is a proven method of achieving power transmission over very long distances. It would play a vital part of the SSG, since it allows power to be transmitted from areas where it is in abundance to areas experiencing a shortage, which would secure the energy supply across the entire region. It would also facilitate the use of offshore wind farms — whose natural location is so distant from areas of electricity demand that HVDC is essential to ensuring efficient transmission.
HVDC also allows power transmission between unsynchronised AC distribution systems. AC systems operate at a set frequency and if these frequencies are different, the systems cannot be connected. HVDC circuits do not have a frequency, eliminating this problem and allowing multiple circuits to be interconnected.
Most significantly, HVDC suffers lower electrical losses than AC transmission. It has a uniform current density throughout the line, so there is no skin effect as there is in AC circuits. Although the corona effect, which is an electrical discharge that appears around a charged conductor, is still generated in a HVDC system, it is considerably lower than in AC systems, facilitating more efficient electricity transmission across the vast area encompassed by the SuperSmart Grid.
CONVERTING BACK TO AC
HVDC is ideal for transmitting over long distances, but when transmitting electricity into the local AC transmission grid, the direct current must be switched back to alternating current using a converter system. All converters, including HVDC converters, generate harmonic distortion to some degree.
If harmonics are not controlled, they can wreak havoc with the transmission system, jeopardising power quality and increasing the chances of equipment malfunction and electrical losses on the line. Therefore, it is important to integrate harmonic filters into the HVDC converter stations to block these unwanted currents.
Harmonic filters allow current at the frequency of the AC network to pass through, while redirecting distorted harmonic currents into a harmonic filter resistor, where they are dissipated as heat. This ensures that the unwanted currents are safely removed from the transmission network in a controlled way, which helps to secure the power supply when converting from DC to AC.
Although the SuperSmart Grid is purely theoretical, it’s clear that the technology necessary to realise this concept already exists. With countries all over the region setting ambitious renewable energy targets, perhaps this could be the solution to providing a secure, sustainable power source across all three continents.