ENABLING GREAT BRITISH ENERGY
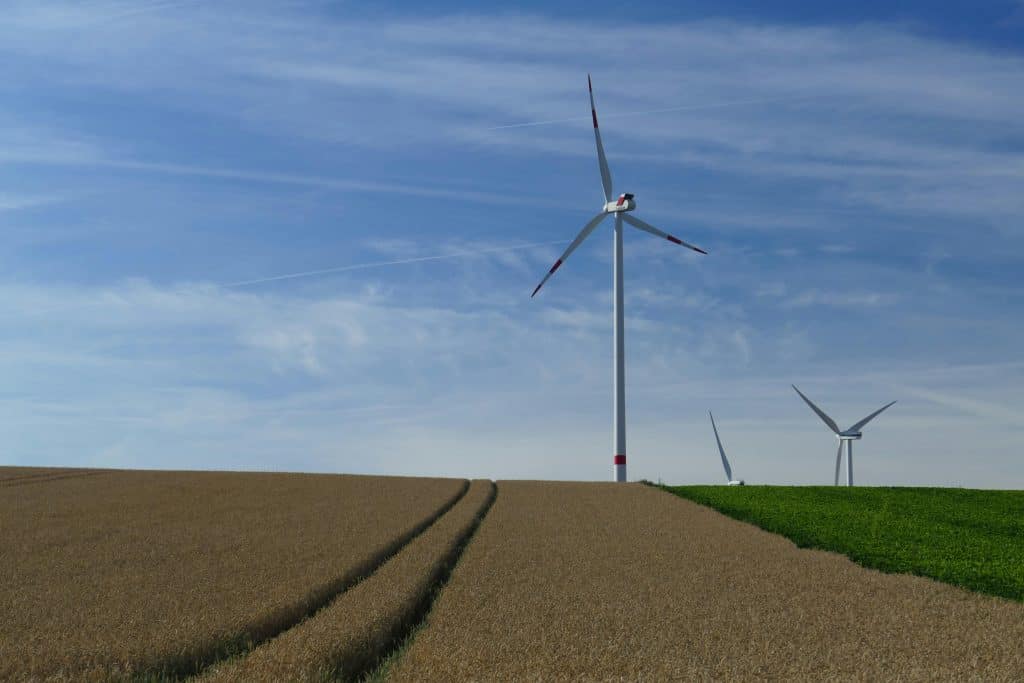
A ZERO-CARBON GRID REQUIRES SPECIFIC TECHNOLOGIES TO ENSURE RELIABILITY
As part of Labour’s plan to boost the UK’s renewable energy production, ‘Great British Energy’ will see the production of a greater number of floating offshore wind farms and tidal power projects. However, for these technologies to be a success, it’s essential to have the right enabling mechanisms in place. Here, Mike Torbitt, Cressall’s managing director, explains the role of resistor technology in making GB Energy a success.
While the exact details about what GB Energy will involve are still uncertain, we can paint a pretty good picture of it from the current information at hand. Starmer’s government intends to invest £8.3 billion of funding into a new, publicly owned green power company as part of wider energy security and sustainability goals.
DELVING INTO GB ENERGY
GB Energy will work with the private sector to provide investment into emerging energy technologies like green hydrogen, floating offshore windfarms and tidal power. It will also scale investment into existing renewable technologies like onshore wind and solar power.
By boosting the UK’s renewable energy power, GB Energy is projected to create 650,000 new jobs across the UK, lower energy bills, increase energy security and create a zero-carbon energy system to the UK by 2030. Labour has pledged to establish GB Energy within its first few months of parliament by passing a new Energy Independence Act, meaning we could see GB Energy materialise by the end of the year.
While the benefits of transitioning to a 100 per cent zero-carbon energy system are abundantly clear, there are certain logistical and technological considerations to make to eliminate fossil fuels from the energy system completely.
THE CHALLENGES OF RENEWABLES
Whether it’s energy from the Sun, sea or wind, renewables have one thing in common — their input energy is extremely variable. For tidal and wind projects, the turbines work in a very similar way, so manufacturers must ensure they can safely manage what can often be high and unpredictable surges of power.
There may be times where winds or waves are so strong that high inrush currents occur. These can result in overvoltages in the system, leading to component damage, or even failure in extreme cases. When renewables like these make up the entire energy system, preventing component failure from scenarios that we know will occur at some point is essential to continuity of supply.
As renewable resources grow in sophistication, it is vital that other systems also keep pace in order to effectively manage the power they create.
GETTING IN CONTROL
Overvoltage issues can be remedied by using resistor technologies, which all work by limiting or regulating the flow of electronic current in a circuit. Depending on the specific renewable application, there are different solutions to prevent overvoltages.
For tidal turbines, a dynamic braking resistor (DBR) can be integrated into the generation and control circuit to protect against any excess power generated by strong currents. Cressall’s EV2 advanced, water-cooled resistor is designed for these applications. The range is modular, so multiple resistors can be combined to handle power outputs up to one Megawatt. The EV2 also boasts an IP56 ingress protection rating, making it able to withstand harsh marine environments and suitable for tidal turbine applications.
In wind turbines, overvoltages are avoided by using a pre-insertion resistor (PIR). Insulated for the full system voltage, PIRs like Cressall’s mitigate against temporary overvoltages, such as those caused by exceptionally strong winds. They also absorb and control transient magnetising currents within transformers throughout the network. This control helps keep voltages consistent with minimal dips, reducing potential disturbances for users of the power network.
While the specifics of GB Energy are still yet to be announced, a fully renewable energy grid is certainly on the cards in the coming years. The industry will need to consider the importance of having the right technology in place to deal with the challenges that renewables bring, and make green energy a viable system nationwide.
CRE660/08/24