THE ROLE OF HVDC IN ENERGY TRANSITION
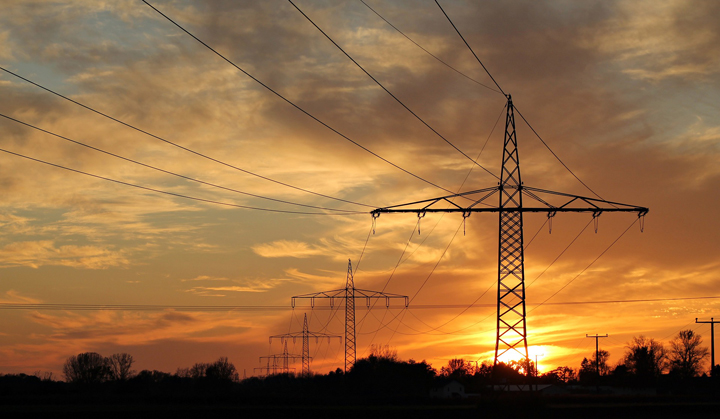
With the rise of offshore windfarms and international grid links, effectively and efficiently transmitting electricity over long distances is more crucial than ever before.
Simone Bruckner, Managing Director of Cressall, explains the role of high voltage direct current (HVDC) and filter resistors in making long-distance energy transition possible.
The UK has four times more offshore windfarms in operation than in 2012, with the number set to rise significantly as the government looks to reach its goal of generating 50 gigawatts (GW) of offshore wind by 2030.
Along with this rise, international and intercontinental grid links have increased as the UK trades excess power with other countries, much of which is generated by renewable means. Trading the surplus not only saves energy, but also prevents Brits paying to turn off turbines when more energy is generated than the grid can take.
As the UK currently has 13.9GW offshore wind capacity compared to its 50GW goal, it is important that this output is used efficiently and energy loss is kept at a minimum. Although alternating current (AC) is standard in electrical power transmission, the current often concentrates near the conductor’s surface – known as the skin effect – which causes energy loss.
HOW HVDC HELPS
HVDC is a transmission system that uses direct current (DC) for the transfer of power over long distances. As remote offshore windfarms and the grid are often far apart, HVDC enables effective transmission due to its uniform current density throughout the line.
Additionally, HVDC supports the trading of excess power between unsynchronised AC distribution systems, which run at a set frequency and cannot be connected to those with a different frequency. As HVDC does not have a frequency, multiple circuits can be interconnected and converted to both system voltage and frequency levels of the system at point of use.
While HVDC is used for international grid links, it must be converted back to AC at the local grid level. However, converters create harmonic distortion, which in turn can cause lower efficiency, overheating and increased chance of equipment failure.
Therefore, harmonic filter resistors are a vital part of HVDC and SVC converter stations, helping to remove harmonics by dissipating them as heat. This ensures a safe and assured power supply for the UK and countries across the continent.
The UK’s rollout of offshore windfarms currently puts it among world leaders, and with the pipeline of projects close to 100GW, Britain could soon supply many countries with surplus energy. With the ever-increasing need for sustainable energy, HVDC ensures that countries across the world can safely and securely benefit from wind power.