POWERING THE SHIFT TO ELECTRIC MINES
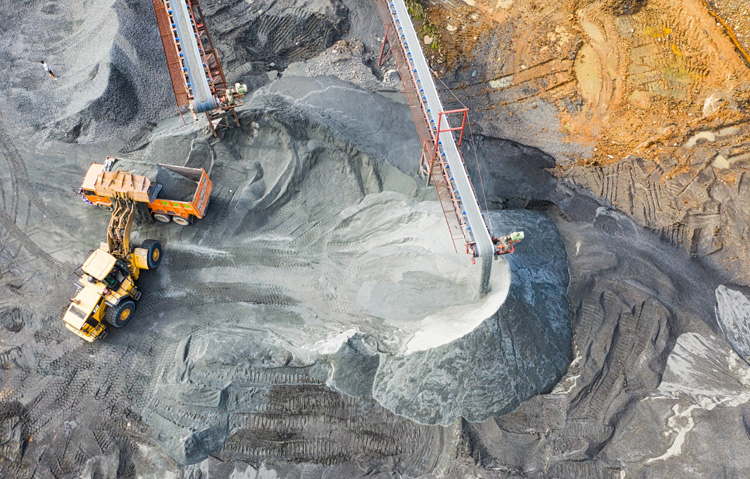
According to a 2020 McKinsey report, the global mining industry is responsible for between four and seven per cent of total greenhouse gas emissions, so any technology that contributes to the sector’s decarbonisation is valuable. For decades, diesel-powered machinery and vehicles have dominated mining. Its long success is down to the fact diesel engines can handle the extremely harsh conditions of underground mines, enabling access to once unreachable depths.
THE PROBLEM WITH DIESEL
Diesel’s power doesn’t come without problems. From an environmental perspective, the use of diesel engines doesn’t support mining’s decarbonisation agenda.
However, there is another reason why moving away from diesel is a good idea — its negative impact on worker safety. According to the International Labour Organisation, despite only employing one per cent of the global labour force, mining is accountable for eight per cent of fatal workplace accidents.
Two major sources of hazard in underground mining are ventilation and noise, which are both worsened by the use of diesel-powered machinery. The emissions from diesel mining equipment are a large contributor to the toxic gases found in underground mines, which require vast, comprehensive ventilation systems to clear the air for workers to breathe. In addition, the noise produced by large diesel engines adds to the noise pollution, which is already significant, and can lead to noise-induced hearing loss.
THE MOVE TO ELECTRIC
EVs eliminate the noise and emission problems associated with diesel power systems. However, currently only 0.5 per cent of mining vehicles are fully electric, and many mines are reluctant to make a complete shift due to performance concerns.
The same worries holding automotive consumers back from changing to an electric car hold true for mine operators, who are reluctant to move away from diesel’s reliability due to concerns around battery capacities.
With operations taking place hundreds, or even thousands, of metres below the ground, underground mining vehicles need to consistently perform well. Equipment failure in underground mines can not only result in huge repair costs and significantly impact production, but it can also risk health and safety, so it is critical that electric mining vehicles can meet the demands of this application.
THE REGENERATION GENERATION
Underground mining equipment encounters some of the harshest conditions out there — unseen holes, tight tunnels and uneven terrain can all place stress on automated equipment. Therefore, vehicles must be designed with these conditions in mind.
An essential component of any EV is its dynamic braking resistor (DBR). Heavy duty applications like mining require heavy duty components to withstand the tough operating conditions they face.
When a mining vehicle brakes, using the principles of regenerative braking, the first option is to store the excess energy produced in the vehicle’s battery for reuse, improving the energy efficiency of the vehicle and keeping the system operational for improved safety.
However, when the battery is close to its full charge, this is not possible. A dynamic braking resistor is the simplest, most reliable and cost-effective solution to this problem as it dissipates the excess energy as heat, allowing the EV to stop when required. This is particularly useful in mining applications, where operational efficiency and reliability are crucial.
Cressall’s EV2 water-cooled DBR has a unique design, meaning it takes up just ten per cent of the volume and 15 per cent of the weight of a conventional air-cooled DBR. Units can be combined in up to five-module assemblies to meet high-power requirements.
Mining techniques have evolved many times throughout its rich history. With increased pressure to decarbonise, mining EVs will play an essential role in bringing the industry into the 21st century, making operations efficient, reliable and safe.